What our customers have to say about working with Project Engineering
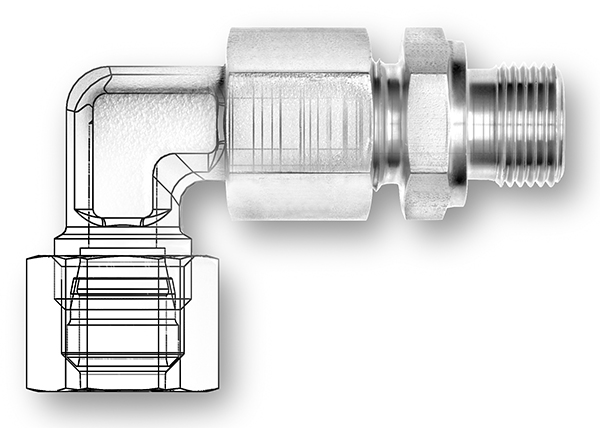
Project process
A practical example of system optimisation
The graphics show a step-by-step system optimisation using a customer example. Costs, assembly time, the number of sealing points and the number of items to be processed changed in the course of the project to suit the customer.
Step 1: functional model
Our customer came to us with the following idea: he wanted to distribute a fluid from one conveying unit to two containers. The connection points of the assembly and the desire to implement this solution with EXMAR products are given. In the first draft, male adaptor fittings with conical threads were used, which were to be sealed with an additional sealant.
Step 2: prototype
In order to guarantee the sealing of the male adaptor fittings and a uniform screw-in height of the assembly even after repeat assembly, we have exchanged the conical for cylindrical threads with sealing edge. Tapered elbow fittings allow easy adjustment of the alignment.
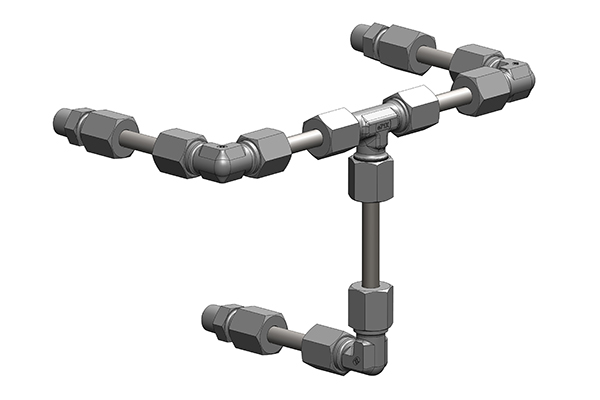
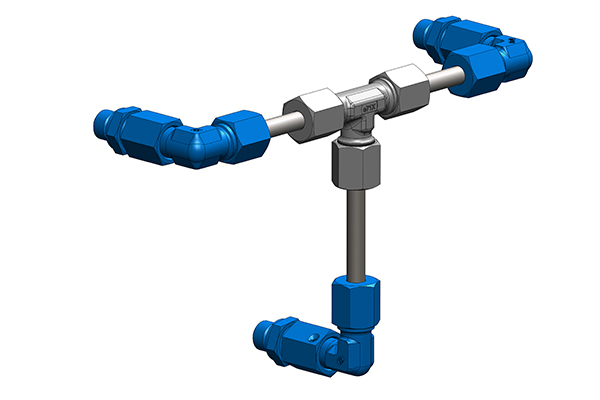
Step 3: series
The final version uses a solder assembly that eliminates both the elbow and central T-fitting. This significantly reduces the number of sealing points. The customer receives this assembly from EXMAR ready for installation.
Evaluation
The graphs show how assembly time, number of sealing points and number of articles to be managed have changed in the course of the project for the benefit of the customer.
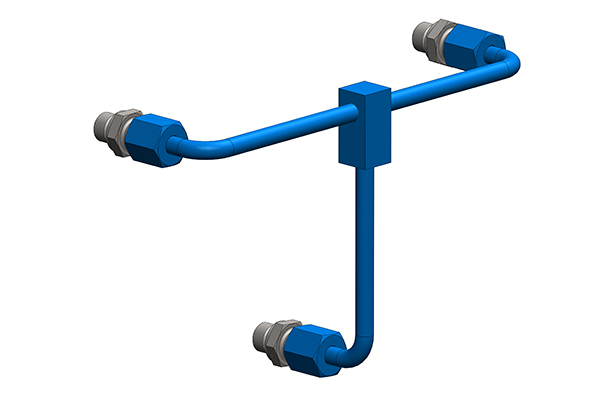
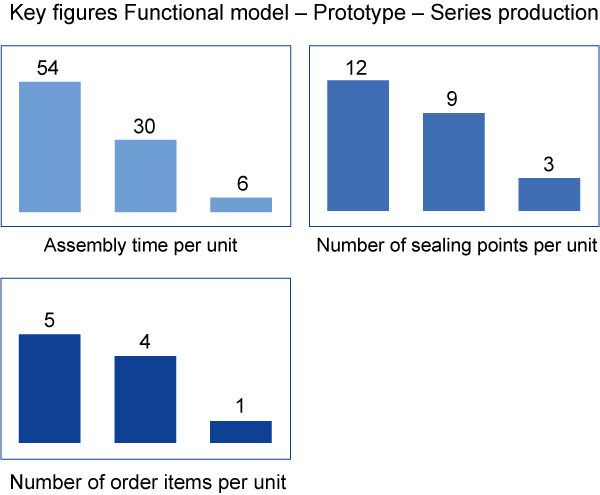